- What is SAP PM?
- Reasons for plant maintenance
- What does SAP PM do?
- Maintenance Plant
- Maintenance Planning
- Technical objects structure
- Preventive maintenance
- Maintenance Processing
- Maintenance Projects
- Work clearance Management
- Information System
- Conclusion
What is SAP PM?
SAP PM module is an SAP ERP Central component which offers support for maintaining the system and equipment. SAP PM refers to the SAP Plant maintenance module. It is software intended for industrial enterprises, where all the major tasks related to the maintenance of technical systems can be represented. This includes but is not limited to inspection, repair and maintenance.
Reasons for plant maintenance
Plan maintenance has three main reasons. They are
Inspection: to determine the actual condition
The inspection will be planned in advance to determine the actual state of the system or the equipment.
Repair: To restore to the optimal condition
Repairs are necessary when the equipment is not able to function properly. When the machinery fails, the production department will send a request to the maintenance department for the repair of the equipment. The maintenance department will investigate and perform the repairs needed.
Preventative: to maintain the present condition
Planned maintenance is programmed to minimize failure maintenance issues. The process makes it possible to identify all the equipment's weak points and conduct regular inspections with minor repairs.
What does SAP PM do?
SAP PM works with technical objects that are used for mapping and structuring the existing plants in the system. An important object is a piece of equipment. SAP uses the term for describing company objects that need to be independently maintained. SAP PM module may be integrated into other SAP modules like SAP material management, sales and distribution, production planning, controlling and several internal and external apps. The integration of PM with other SAP modules allows you to update the data and process the information required for the PM module. The following steps illustrate a work order notification process and how it will be performed as part of plant maintenance.
- Notification
- Recently created work order
- Create a request to purchase work orders
- Buy order created, and the parts received
- Work Order parts issues
- Approve and plan the work order
- Scheduling and releasing the work order
- Carrying out the work order
- Completion of a work order
To efficiently manage SAP maintenance activities within an organization, we must separate the existing maintenance structure from technical objects. Technical objects help to define what types of machines exist in an organization, and with the help of the features of the object, we may define other technical objects in more detail. To demonstrate the technical objects in the system, we must be familiar with the planning and structure of maintenance in the organization. It involves the activities of defining a maintenance plant and maintenance planning of the system.
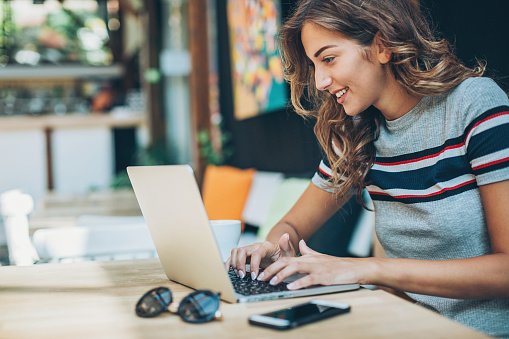
SAP PM Training
- Master Your Craft
- Lifetime LMS & Faculty Access
- 24/7 online expert support
- Real-world & Project Based Learning
Maintenance Plant:
The maintenance plant of a technical object is called the plant, where we carry out the maintenance tasks of the objects, and the planning is carried out. Following are the activities involved in the Maintenance planning plant:
- Set the task list according to the maintenance plan
- Perform material planning according to the tasklist BOM
- Managing and scheduling maintenance plan
- Creating and performing maintenance orders
Maintenance Planning:
In accordance with the organizational structure, maintenance planning must be done. We can define maintenance planning tasks according to the defined technical objects and structure. Following are the types of maintenance planning:
- Centralized Maintenance Planning: Central planning within an organization will support the following structures:
- There will be one plant for all technical objects that is the maintenance planning plant and the maintenance plant.
- In other cases, the organization may have several maintenance plants, but there will be a plant where maintenance planning is done.
- Decentralized Maintenance Planning
In this case, the organization is composed of several plants, and every plant serves as its own maintenance planning plant. In the SAP system, every plant is listed as a maintenance planning plant.
- Partially Centralized Maintenance Planning
In partially centralized maintenance planning, an organization is made up of several plants, some of which serve as maintenance plants and maintenance planning plants, whereas other plants may be used as maintenance planning plants. Plants that are not involved in maintenance planning are allocated to the other maintenance planning plants.
Technical objects structure:
Various kinds of structures may be used for technical objects depending on the organizational structure.
Functional structure: In a functional structure, the technical system is divided according to the functional locations. Dividing the product range into functional locations allows a single unit to act as functional locations within the system.
Object related structuring: This structure divides the technical system into so-called pieces of equipment. Equipment is a single object that may be placed within a technical system or a part of that technical system.
Subscribe to our YouTube channel to get new updates..!
Functional and object-based structuring: This is the combination of both functional and object-based structuring by means of equipment and is divided according to the functional location. The functional location indicates where the technical tasks are carried out, and the equipment indicates the purpose with which the tasks must be carried out. That is, a functional location is an organizational unit which serves to maintain a company's objects according to the functional area, spatial criteria or process-related. A functional location indicates the location where a maintenance task must be carried out.
Preventive maintenance:
Preventive maintenance is expected to maintain the long-term high availability of the technical systems, such as production plants.
Maintenance Processing:
There are several levels of maintenance processing that do not need to be fully implemented. This makes it possible to process a repair through a number of planning stages like material provision, preliminary costing, resource planning, work schedules, and permits. However, it can respond immediately to events that cause production to stop and produce the necessary orders and store papers with minimal entries as soon as possible.
Maintenance Projects:
The purpose of this component is to Perform maintenance tasks through revisions and through project system functions. Here we may assign maintenance orders to the projects so that they can be included in the project structure. Maintenance orders can be assigned to networks for detailed scheduling.
Budget Planning for Customer service and Plant Maintenance:
SAP Business Information Warehouse offers budget planning features for plant maintenance and customer service. Budgets may be planned using a zero-based or historical-based budgeting approach. In zero-based budgeting methodology, the budget is created using planned data, in especially the simulated planned costs and the quantities. Data from task lists, maintenance plans or ad hoc are used as a basis of this approach. In plant maintenance, this budgeting methodology according to planned data is referred to as zero-based budgeting. In a history-based budgeting approach, the budget is calculated based on actual historical costs.
Work clearance Management:
Required maintenance of technical objects, like inspections, preventive maintenance or repairs, shall be carried out only after all measures to ensure a safe workplace have been implemented. These security measures may include but are not limited to fire protection, lockout/Tagout, and radiation protection. In the case of lockout/labelling, the technical objects are electrically isolated or mechanically separated from the other parts of the technical system when the maintenance work or the special tests are carried out. The work on these technical objects may then be done in a secure manner.
Information System:
The Plant Maintenance Information System may be used at various levels in the decision-making process as a tool to monitor, control and plan the business operations. Information System is a flexible tool to collect, aggregate and evaluate plant maintenance data. The information system allows us to view all the information of the operative application in many ways. We may also define the level of detail where you would like to view the information.
Conclusion:
In this tutorial, we have learned about all the basic details of SAP Plant management, why we need it, how SAP PM works, and Technical objects structure. We hope you found this information helpful. If you are searching for any other topics related to SAP PM, comment your query below. We will get back to you with the answer.
About Author
Kavya works for HKR Trainings institute as a technical writer with diverse experience in many kinds of technology-related content development. She holds a graduate education in the Computer science and Engineering stream. She has cultivated strong technical skills from reading tech blogs and also doing a lot of research related to content. She manages to write great content in many fields like Programming & Frameworks, Enterprise Integration, Web Development, SAP, and Business Process Management (BPM). Connect her on LinkedIn and Twitter.
Upcoming SAP PM Training Online classes
Batch starts on 26th Aug 2025 |
|
||
Batch starts on 30th Aug 2025 |
|
||
Batch starts on 3rd Sep 2025 |
|